顶出机构的设计需保证压铸件能够平稳、可靠地脱模,顶针的布置应均匀分布在压铸件的受力部位,避免因顶出力不均导致压铸件变形。顶针的数量和直径根据压铸件的重量和尺寸确定,顶针与模具的配合间隙应合理,既要保证顶针运动灵活,又要防止金属液泄漏。对于薄壁或易变形的压铸件,可采用顶板、顶管等顶出方式,增大顶出面积,减少压铸件的变形。自动压铸模具的自动化集成设计是实现自动化生产的关键,需与压铸机的自动化系统相匹配。取件机械手的夹持方式和运动轨迹应根据压铸件的形状和取出位置设计,确保取件平稳、快速;喷涂机构的喷嘴位置和喷涂范围应覆盖整个型腔表面,喷涂量需均匀可控;传感器的安装位置应能准确监测模具的工作状态,如合模位置、顶出位置、型腔温度等,以便及时反馈信息并进行调整。模具分型面密封采用O型圈+石墨垫双重结构,防止金属液飞溅。北仑区压铸模具
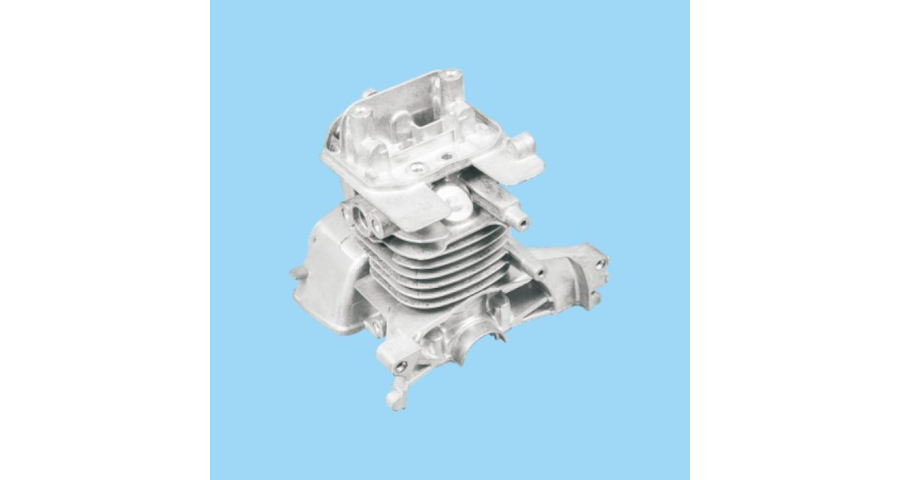
航空航天领域对零部件的质量、性能和可靠性要求极为严苛,精密压铸模具在该领域的应用正不断拓展。在航空发动机制造中,精密压铸模具用于生产叶片、机匣等关键零部件。以航空发动机叶片为例,其形状复杂,对精度、强度和耐高温性能要求极高。精密压铸模具通过先进的设计与制造工艺,能够精确成型叶片的复杂曲面,保证叶片的空气动力学性能。同时,采用高温合金材料与特殊的热处理工艺,使叶片具备良好的高温强度和抗热疲劳性能,满足发动机在高温、高压、高转速等极端工况下的工作要求。宁波加工压铸模具公司压铸模具的快速换模系统可缩短停机时间,提高生产效率,适应大规模生产需求。
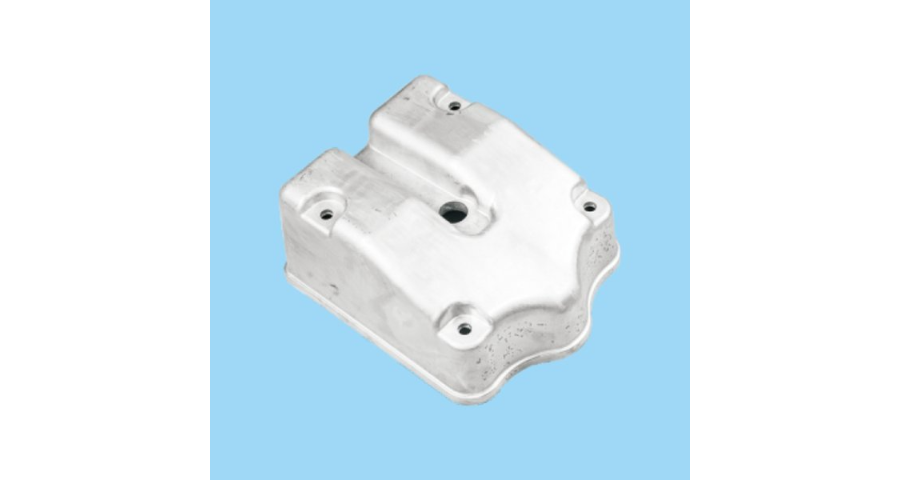
热疲劳裂纹是压铸模具在长期使用过程中面临的另一个严峻挑战,它如同隐藏在模具内部的 “隐形***”,逐渐侵蚀着模具的寿命。在压铸过程中,模具表面反复承受高温金属液的加热和冷却介质的冷却,这种频繁的热循环会使模具表面产生交变热应力。当热应力超过模具材料的疲劳极限时,模具表面就会逐渐产生微小的裂纹,这些裂纹会随着压铸次数的增加而不断扩展、连接,较终形成热疲劳裂纹。热疲劳裂纹的出现不仅会影响模具的外观,还会降低模具的强度和密封性,导致铸件出现飞边、毛刺等缺陷,甚至使模具提前报废。
从工艺本质来看,自动压铸模具利用高压将熔融状态的金属液压入模具型腔,使金属液在型腔内快速冷却凝固,从而形成与型腔形状一致的金属零件。其重心特点在于 “自动”,即从金属原料的加入、熔融,到压射、保压、开模、取件、模具清理等环节,均通过预设程序和自动化机构完成,减少了人为因素对生产过程的干扰。根据所加工金属材料的不同,自动压铸模具可分为铝合金自动压铸模具、锌合金自动压铸模具、镁合金自动压铸模具等;按照模具的结构形式,又可分为单型腔自动压铸模具和多型腔自动压铸模具,单型腔模具适用于大型或高精度零件的生产,多型腔模具则能一次成型多个零件,提高生产效率。压铸件尺寸精度可达CT4-6级,依赖模具的高精度加工与装配。
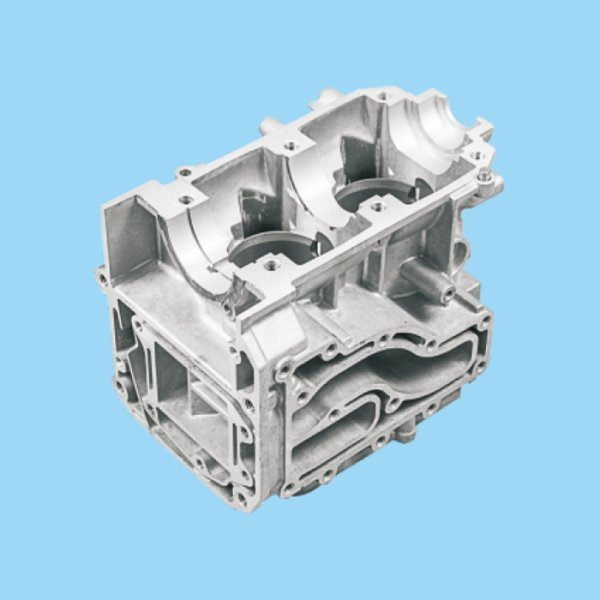
当压铸件完全凝固后,压铸机的开合模机构带动动模后退,实现开模。开模到一定位置后,压铸机的顶出机构通过顶杆推动模具的顶针板,使顶针伸出,将压铸件从型腔中顶出。同时,取件机械手动作,将顶出的压铸件取出。取件完成后,喷涂机构向型腔表面喷涂脱模剂,为下一次压铸做准备。对于产生的浇口、流道等凝料,由废料处理装置进行收集。随后,模具再次进入合模阶段,开始下一个工作循环。整个过程通过压铸机的控制系统与模具的自动化辅助部件协同工作,实现了从金属液填充到压铸件取出的全自动化操作,生产效率高,且产品质量稳定。模具设计遵循DFM原则,确保铸造工艺性与后续机加工成本较优平衡。北仑区汽车压铸模具供应
模具的型腔需定期清理,以防止金属残留影响铸件质量。北仑区压铸模具
除了氮化处理和镀硬铬处理外,还有许多其他先进的表面处理技术在压铸模具领域得到了广泛应用。例如,物***相沉积(PVD)技术,它能够在模具表面沉积一层具有特殊性能的薄膜,如TiN、TiCN等,这些薄膜具有高硬度、高耐磨性和良好的化学稳定性,能够显著提高模具的表面性能。化学气相沉积(CVD)技术则是通过化学反应在模具表面形成一层坚硬的涂层,如TiC、Cr3C2等,这层涂层能够有效地提高模具的抗磨损和抗腐蚀能力。此外,还有激光表面处理技术,它通过激光对模具表面进行快速加热和冷却,使模具表面的组织结构发生改变,从而提高模具的表面硬度和耐磨性。这些先进的表面处理技术为压铸模具的性能提升提供了更多的选择,能够满足不同领域对压铸模具的多样化需求。北仑区压铸模具
文章来源地址: http://wjgj.cmgdjgsb.chanpin818.com/mojuog/yazhumo/deta_28744550.html
免责声明: 本页面所展现的信息及其他相关推荐信息,均来源于其对应的用户,本网对此不承担任何保证责任。如涉及作品内容、 版权和其他问题,请及时与本网联系,我们将核实后进行删除,本网站对此声明具有最终解释权。